The Rise Of Men’s British-Made Shoes

http://teqmag.blogspot.com/2014/10/the-rise-of-mens-british-made-shoes.html

Built to last a lifetime, English shoes are designed to be repaired over and over again, and perfectly complement the more refined, tailoring based form of dress that today’s style-conscious gent favours.
To fulfil this worldwide demand, companies such as Church’s and John Lobb are expanding their manufacturing bases in the traditional home of British shoemaking, Northamptonshire. UK Plc is seeing a renaissance in home-grown manufacturing, which can only be a good thing.
Church’s recently announced they were starting work on expanding their St James factory. The two new plots of land will allow the 110,000 square foot factory to add a 130,000 square foot extension, doubling the manufacturing plant, meaning that it will increase its capacity from 250,000 to 300,000 pairs of shoes per year. Church’s already employs 650 people, with another 150 new jobs set to become available after this expansion.
Northamptonshire: The Home Of Shoemaking
The English town of Northampton was once the shoemaking capital of Europe, with 2,000 individual bootmakers working there towards the end of the nineteenth century. The town’s central position and proximity to the eleven rivers running through the county made Northampton an obvious place for cobblers to set up business.
The subsequent availability of leather and Northampton’s strategic importance led to it becoming a centre of military bootmaking, with demand soaring due to the Napoleonic Wars of the late eighteenth and early nineteenth centuries.


The expansion means John Lobb can take on further staff, which will bring the total workers employed in their Northampton factory to over 100. Production will expand steadily to around 40,000 pairs a year.
A Sign Of Quality: Goodyear Welted Construction
The most famous Northampton technique is the ‘Goodyear welted’ shoe. Invented in 1869 by Charles Goodyear, Jr., the Goodyear welted process is the footwear equivalent of the off-side rule: until somebody sits you down and talks you through it, it’s quite hard to understand.The process involves approximately 75 components and 200 separate operations. On average, the whole process, from start to finish, takes eight weeks to complete. The main benefit of footwear that is made using Goodyear welted construction is that it can be resoled repeatedly, giving the shoe a longer lifespan.
Essentially, the upper part of the shoe is shaped over the last and fastened on by sewing a leather, linen or synthetic strip – known as the ‘welt’ – to the inner and upper sole. The welt forms a cavity which is then filled with a cork material.
The sole is then attached to the welt of the shoe by some combination of stitching along the edge of the welt and sole itself, and a high strength adhesive like contact cement or hide glue.
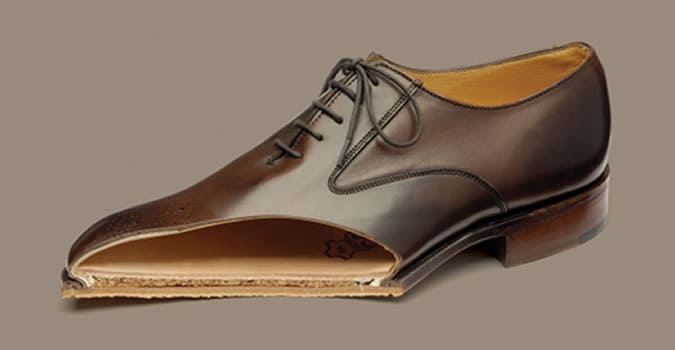


Yet while England may be famous for the Goodyear welted shoe, he adds that there are other construction processes to look out for:
“There are many other constructions, all with different benefits, for example: moccasins can be very light and flexible, but are not so durable or as well-suited to bad weather. Cemented-soled shoes can look very sleek, but will not feel so sturdy when walking on rough ground, will be less water-resistant and harder to repair.
Blake-stitches shoes have the soles stitched directly to the insoles. This means that, as the shoes are flexed, they can start to leak through the stitch holes. In our opinion, welted shoes provide a kind of ‘best of all worlds’ solution.”
Post a CommentDefault CommentsFacebook Comments